PATENTS
FMS (Floating Mount System)
This is a stress-free system for fastening the table to the frame, which is characterized by free thermal expansion of the table top. This solution is mainly dedicated for large-size constructions, in which the materials of the frame and table differ significantly in terms of thermal expansion coefficients, e.g.: steel frame and aluminum table.
The table is fixed on three supports on the Z axis, and fixation occurs on the Z axis by means of flexible elements in such a way that the flexibility is oriented on the XY plane. Such a system of positioning and fixation leaves three degrees of freedom, which ensures stress-free thermal work during expansion of materials under the influence of temperature. The floating table – if necessary – may additionally be fixed by removing one to three of the remaining degrees of freedom – e.g. if it is necessary to combine several frame+table constructions into a single system.
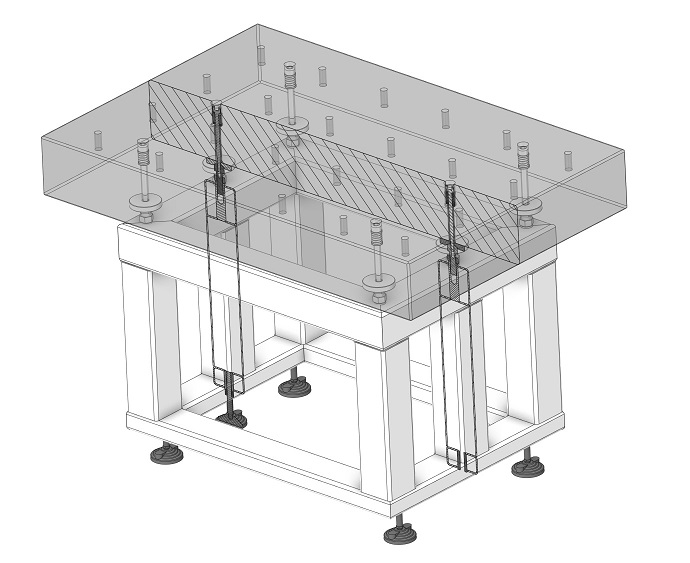
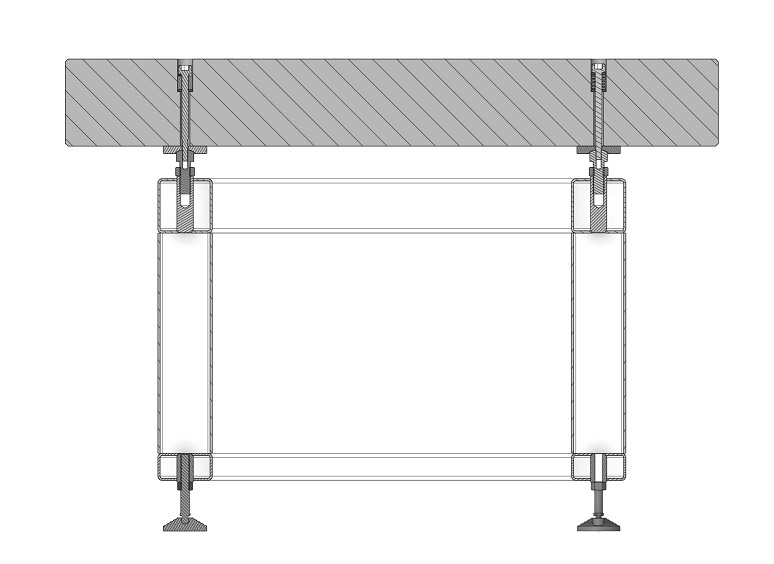
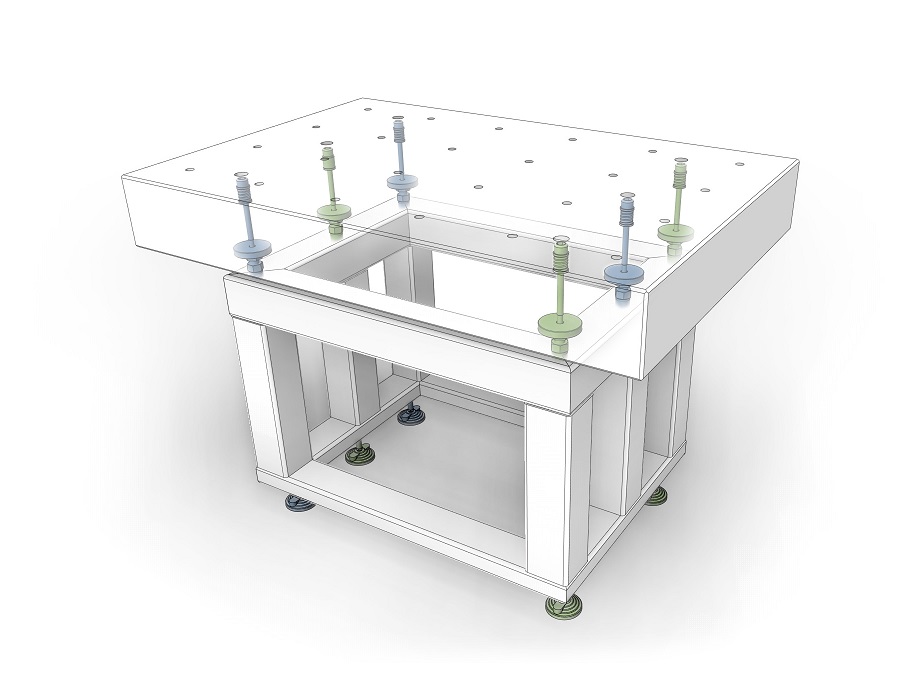
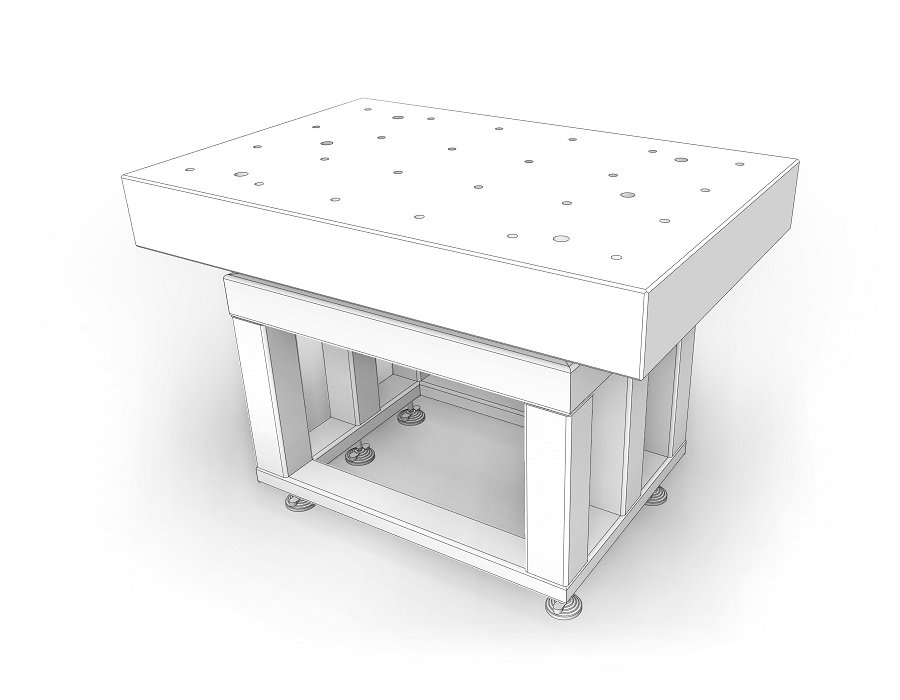

PL (Programming Light)
Our innovative solution is a programmable informational lamp. With the right interface at their disposal, the user is able to program light messages depending on selected events. This solution differs from the classical one commonly used in machines, because it is possible to define new operating states of the system besides the three most common ones (green, orange, red). For example, blue as an expansion of green in the case where the process is being performed correctly but one of the controlled parameters is close to the limit value.

The user may also program so-called “interjections” in the form of single, short pulses. For example, during normal operation, the system may inform of the appearance of a special message to be read by means of a one-second-long orange light.
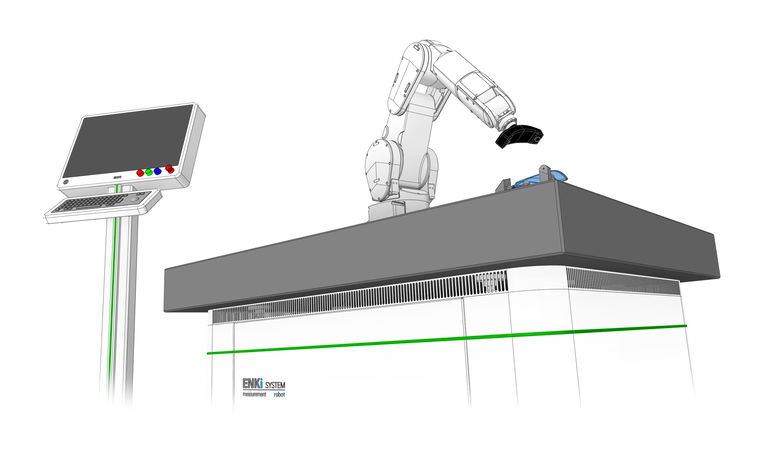

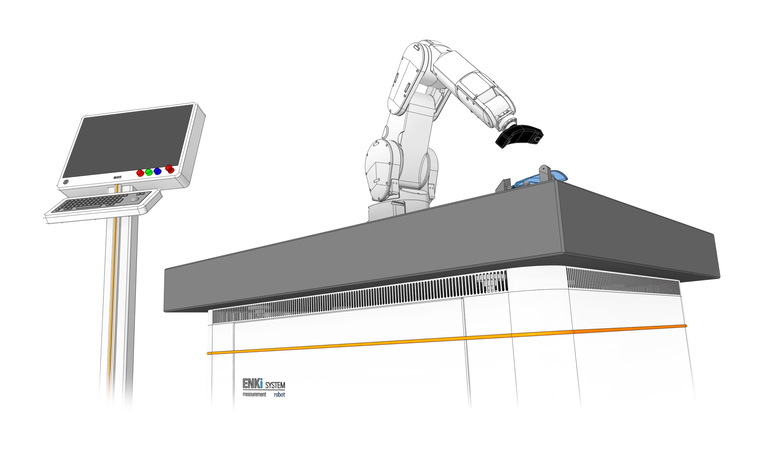
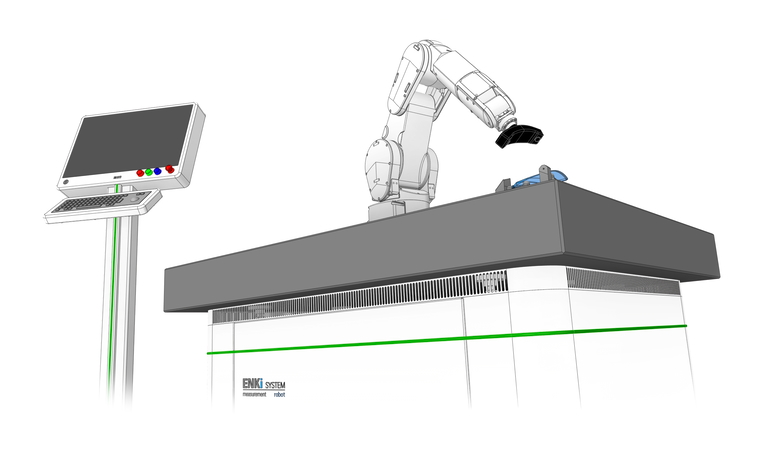
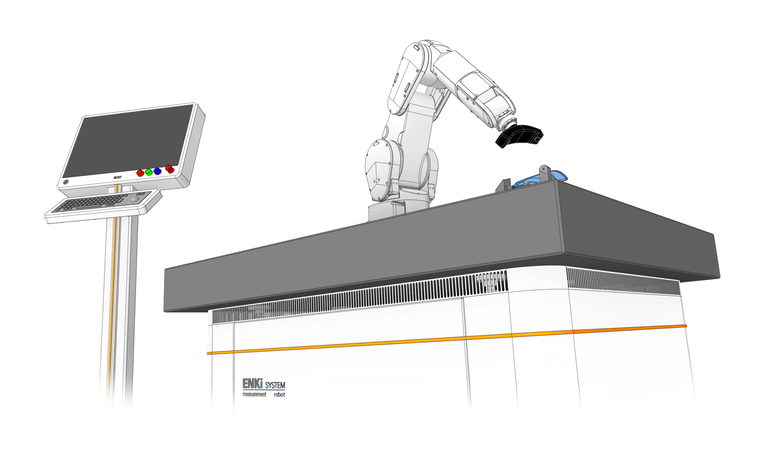
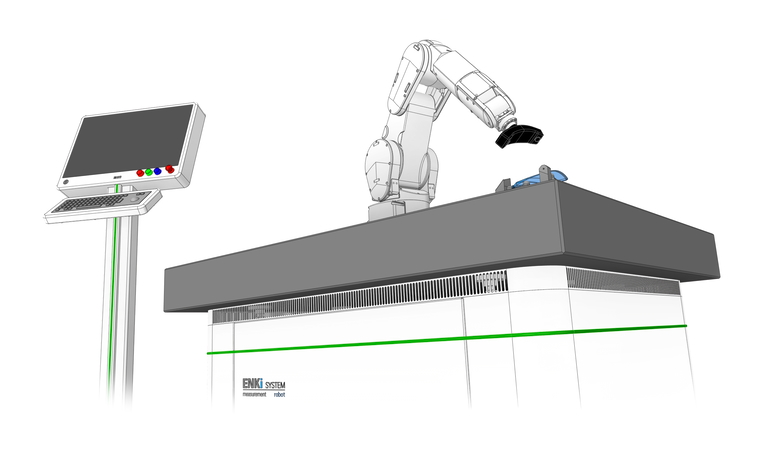
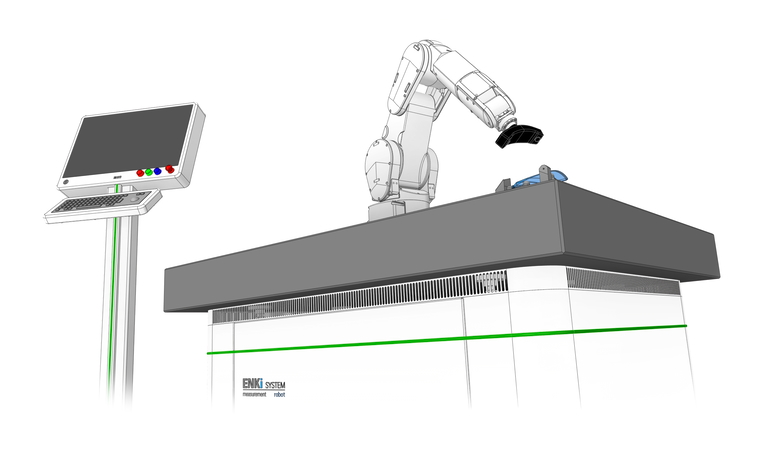
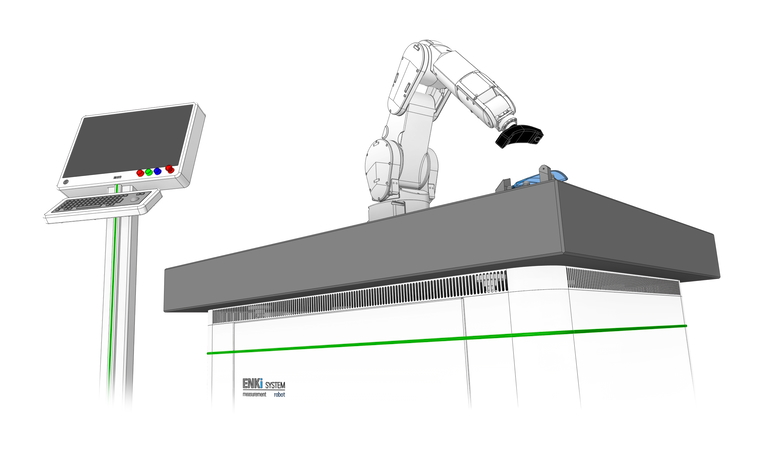
TC/FTC (Temperature Compensation/Flexible Temperature Compensation)
Temperature compensation systems are commonly used in various types of equipment and machinery. However, these systems are designed for specific design solutions – they are non-editable. FTC is an interface enabling definition and edition of any temperature correction chain. The interface may be used only for existing machines, equipment, instruments, etc. – on a one-time basis, meaning that a once-defined object is implemented in any design solution, but is dedicated, in particular for solutions with a design that varies over time.
These are, e.g. machines whose workspace is modifiable and changes depending on needs concerning the grips, tools, manipulators, robots, instruments, etc. installed in this space. Modifications of this type always interfere with the geometry of the workspace and the type of materials comprising this workspace, and this requires the creation of a new temperature compensation model. For example, such compensation systems in machine tools do not account for instruments and the workpiece, and because of this, thermal deformations of the workpiece are omitted in processes performed at variable temperatures. FTC will enable re-definition and editing of compensation models and their recording in a table for reuse.
Example of application.
Measuring table equipped with robotic measuring arm and with measured object fastened in grip.
Due to the use of different materials, under the influence of temperature, the tip of the measuring sensor will move thermally by a different value than the measured point, and variability of temperature during measurements additionally complicates this problem.
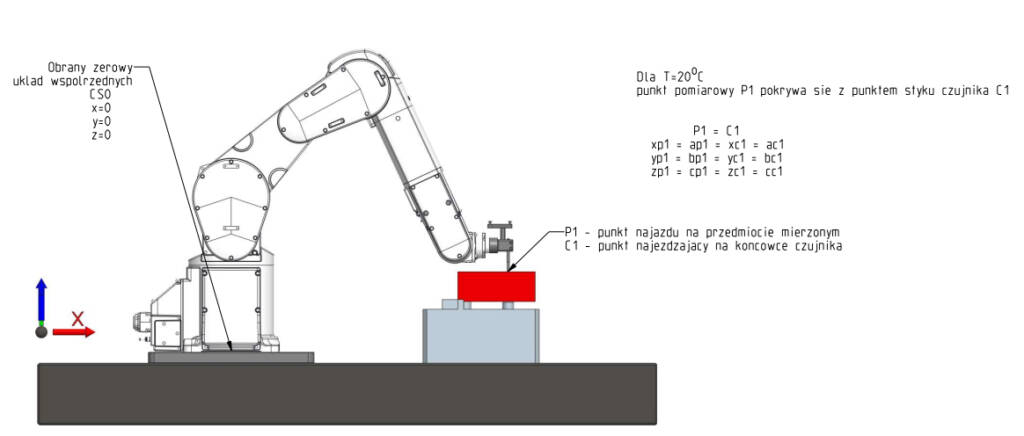

The state of the measuring system at point P1w, at calibration temperature, e.g. 20oC, is presented above. In such a system (after calibration), the point of contact of sensor C1 overlaps with measuring point P1, and all xyz position coordinates overlap appropriately. If this system is subjected to a temperature of, e.g. 40oC, then point P1 will move by a different value than point C1, as presented in the simulation below:
e.g. for the X and Z axes:
Summation of X, Y and Z vectors:
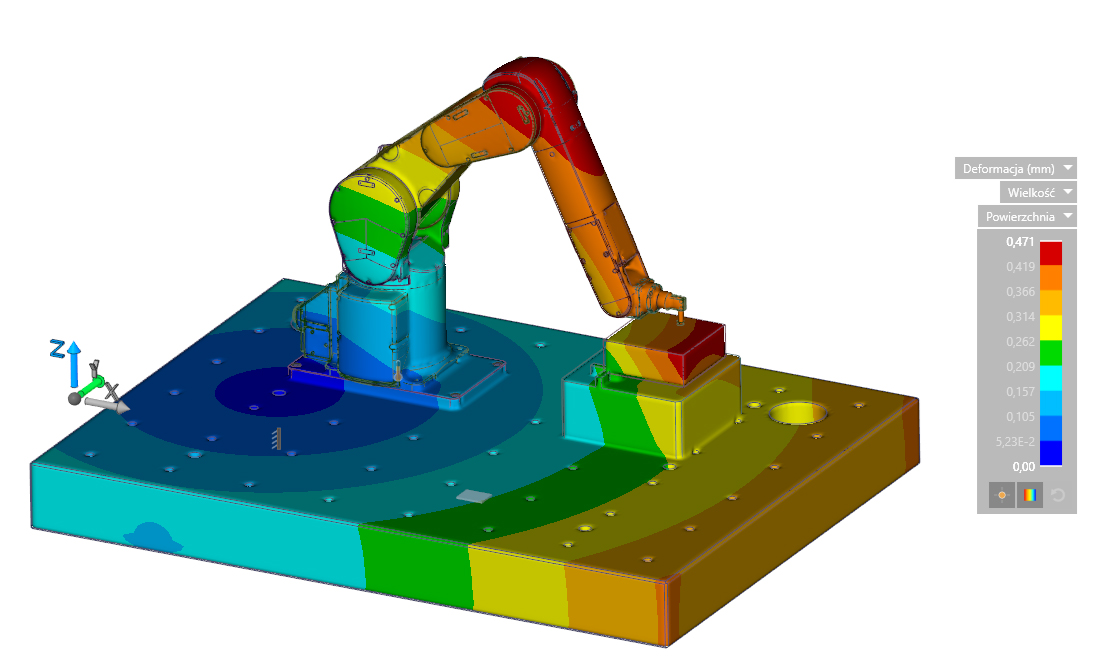
Determination of the temperature compensation chain, under the assumption that the robot arm heats up uniformly, will be as follows:
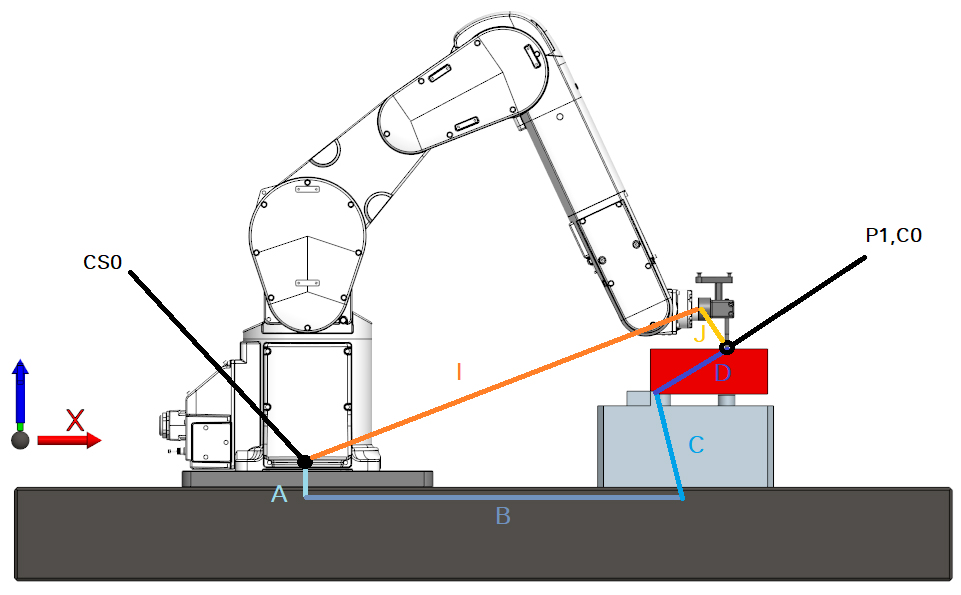
FTC, through its interface, enables modification of the chain in the case where elements significant from the perspective of thermal expansion appear within it. In the discussed example, this may be the application of a robot whose design is based on different materials.
E.g. a Scara-type robot whose Z axis is typically made of steel. Substitution at the discussed station of a six-axial robot with a four-axial scara boils down to modification of the compensation chain for the robot itself by the additional vector I2 :
Similarly, the situation requires modification of the compensation chain when a different type of base plate, body, fastening instrument or basing method is used, which have the effect of changing vector application points, directions and lengths.
The compensation chain may also require the introduction of additional vectors in monolithic elements or assemblies of equipment/machines based on a mono-material construction, but having different thermal expansions due to differing temperature increments ∆T. These varied increments may arise from non-uniformly distributed external and internal heat sources. For example, robot axes that heat up differently due to the greater intensity of movement of a certain axis or installation on these axes of drives of varying power. In such a case, the compensation chain may be as follows:
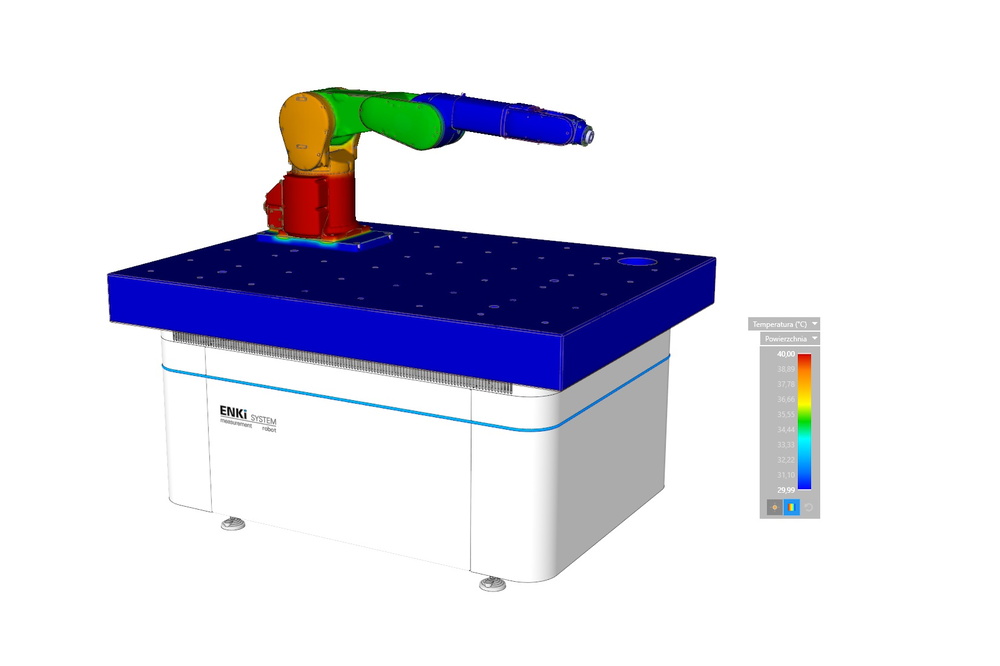
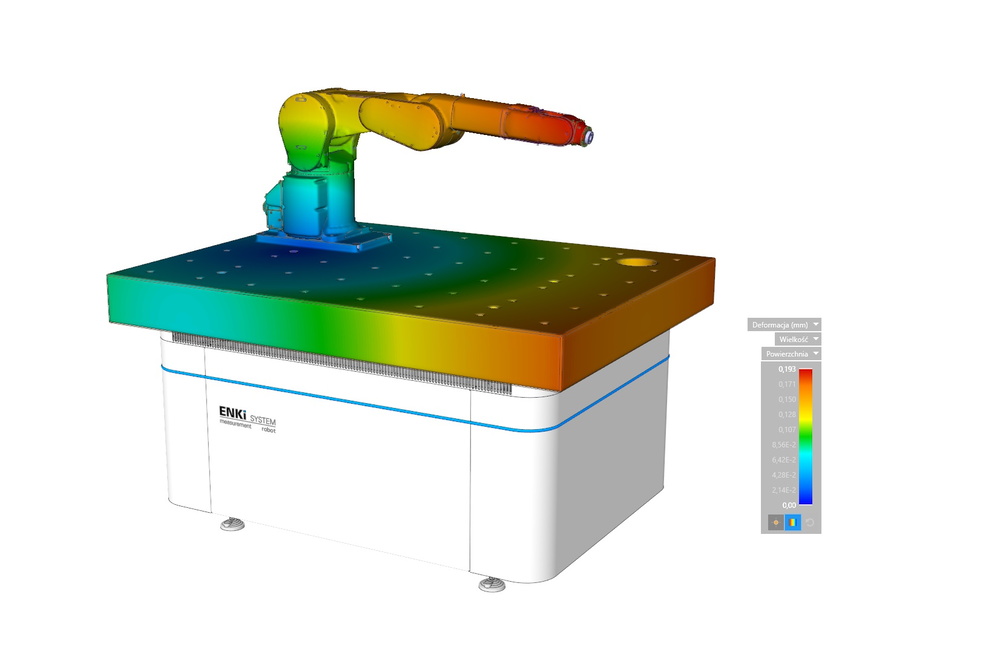